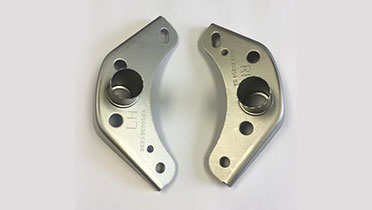
Precision Antilock Brake Assembly
One customer required a precision assembly to encase a critical sensor to monitor wheel movement.
Learn More >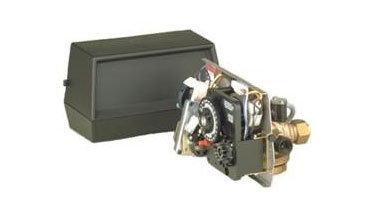
Cost Effective Water Valve Components
The Vulcan team can produce a variety of customized, internal parts for water valves. Look at this case study to see how we accomplished this for one of our clients.
Learn More >
Cost-Effective Welding of Dissimilar Materials
A leading lithium-ion battery manufacturer needed help to weld dissimilar materials and reduce cost.
Learn More >
Cont. Impv.
Experts at identifying and resolving manufacturing inefficiencies, we helped a customer minimize recurring defects from our tubing supplier.
Learn More >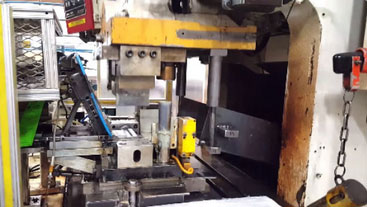
Cost-Efficient Tube Forming Process Improvements
Tooling redesign increased our output by 80% while significantly reducing our customers’ costs.
Learn More >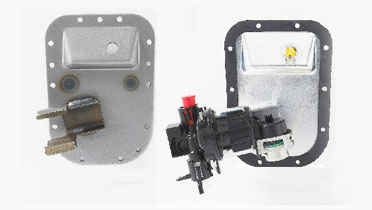
Successful Fueling System Development
We helped the world’s largest manufacturer of heavyweight motorcycles develop two products for use on new models.
Learn More >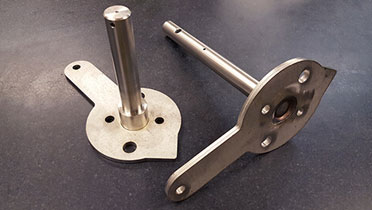
Lower Cost Stainless Steel Spindle Assembly for Eaton Cooper Power Systems
We helped a prominent manufacturer of vacuum fault interrupter switchgears reduce their parts requirements, and consequently, assembly costs.
Learn More >
Cost-Efficient Increase of Tube Feed Cell Production
To increase tube feed cell production capacity in a cost-efficient manner, we developed a manufacturing cell capable of forming multiple sizes of steel or aluminum tubes.
Learn More >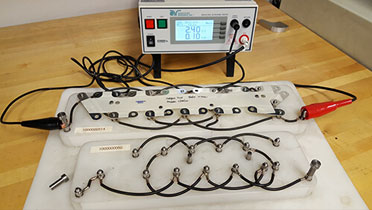
New and Improved Battery Busbar Assembly
Utilizing our tooling expertise, we assembled a newly-designed product for our customer in a cost-efficient manner.
Learn More >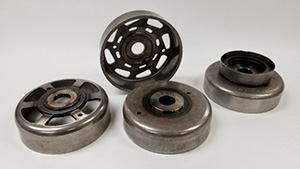
Higher Quality, Lower Cost Spring Cover Assembly
Using our engineering expertise, we helped the world’s largest manufacturer of heavyweight motorcycles improve product quality while reducing assembly costs.
Learn More >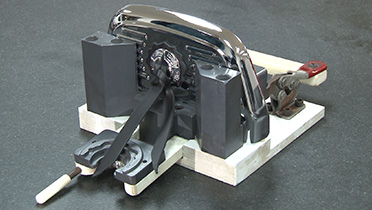
Softail Footboard Manufacturing Improvements
We re-engineered an assembly fixture to reduce operator fatigue and provide our clients in the motorcycle industry with faster turnaround and enhanced quality.
Learn More >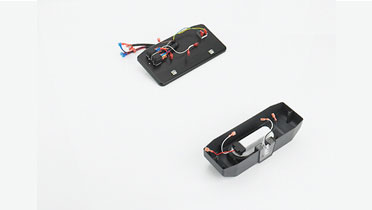
Design and Assembly of New Lighting System
We assisted a manufacturer of independent living aids with design improvements for enhanced quality and performance.
Learn More >
Laminated Plunger Manufacturing Process
We designed a cost-effective, alternative manufacturing process to help a customer produce high-quality actuator plungers with standard steel.
Learn More >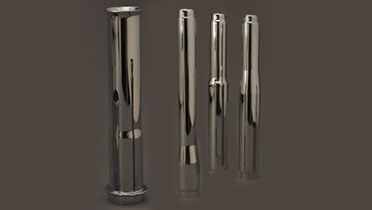
Automating Pushrod Tube Polishing for Harley Davidson Motor Co.
A market leader in the power sports industry needed help automating their metal polishing process and increasing their production capacity.
Learn More >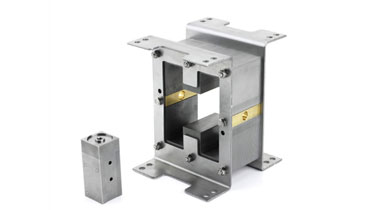
Automated Laminated Actuator Frame Assembly
We helped a leading power distribution and circuit protection manufacturer resolve their existing quality issues.
Learn More >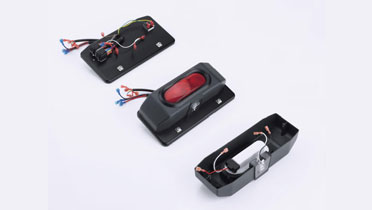
Design for Assembly
A container Kanban system was implemented to provide complete tested assemblies as required using weekly Customer pickups.
Learn More >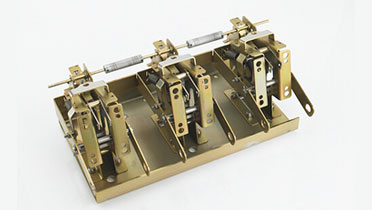
Cost-Effective EMS Mechanisms
We helped a global leader in the power distribution and circuit protection vertical develop two new cost-effective EMS mechanisms.
Learn More >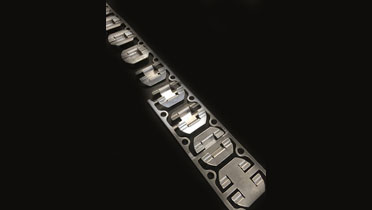
High Speed Stamping
Design a stamping die to produce a part with multiple features such as trimming, coins and forms in a single progressive stamping die.
Learn More >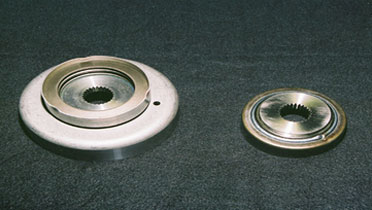
Robotic M.I.G. welded Powertrain Component
Develop a robotically M.I.G. welded joint that would eliminate an assembly operation, reduce freight costs, lead time and inventory.
Learn More >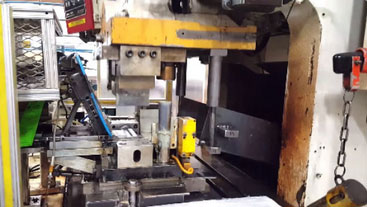
Automated Tube Cut Off and Forming Project
Design and build new tooling that combined several forming operations into once cycle and develop an automated feed system.
Learn More >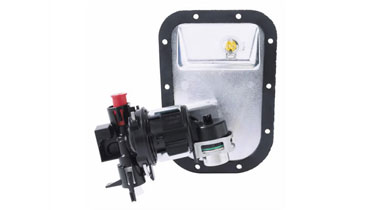
Welded Metal Stamping Assembly
Using low carbon spring steel and subsequent heat treating process we were able to robotically fillet weld the two components
Learn More >