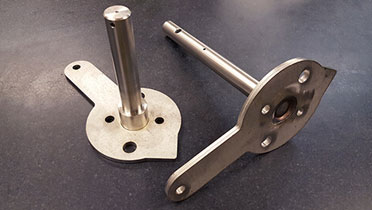
The experienced team at Vulcan Industries Corporation produces high-quality, robotically welded, stainless steel assemblies for OEMs in the electrical power and distribution industry. The following case study demonstrates how we helped a prominent manufacturer of vacuum fault interrupter switchgears reduce their parts requirements, and consequently, assembly costs.
Project Overview
• Industry: Electrical power switch gear and distribution
• Processes: CNC machining prototypes, laser cut blanks, CNC turned components, robotic welding, destructive testing
• Company Background: A prominent manufacturer of vacuum fault interrupter switchgear
• Challenge: Redesigning a product to reduce costs while improving quality with additional enhancements
• Assessment: Initial product review with the purchasing representative raised the question about the purpose of a second component referred to as a spacer. As they did not know how the two parts interacted with each other, we were asked to contact the project engineer.
The Vulcan Solution: Product and Packaging Design Review, Parts Reduction, Robotic Welding Process
Our customer was redesigning a product line. Their goal was to create an enhanced version of an existing system while reducing costs. A brief discussion on spacer use revealed that its only purpose was to provide a flush surface for a mating component rather than adding a machining operation to provide clearance for the weld fillet. Additionally, we discovered that the second version of this assembly was in the design phase, and that both versions would ship to two different locations— Olean, New York, and Queretaro, Mexico. The special protective packaging needed was not considered in the quote request.
We presented a proposal which demonstrated how the Vulcan team could provide assemblies that would not require the spacer, and still have flush surfaces on both sides (no weld fillet protrusion). We recommended recessing the shaft in the bell crank handle and weld, opposite the side originally proposed. A distinct advantage of robotic welding lies in its ability to closely control the amount of wire feed, shielding gases, and voltage. This results in a very controlled fillet size; no protrusion beyond crank handle surface, proper penetration (strength), and consistency. The customer accepted our new model and quickly revised their design.
Our second proposal was for packaging both versions. We worked with our packaging materials supplier and designed a solution suitable for shipment to both customer locations, ensuring the machined surface on the shaft remained protected. This proposal was also accepted.
The Final Result – 2 High-Quality Solutions, Significant Cost Reduction
We provided our customer with two versions of a high-quality product that surpassed their design requirements for impact and load bearing, while eliminating a component that was not required. This brought costs down even further than they had hoped.
At Vulcan Industries, we are experts at reducing product manufacturing requirements, performance inefficiencies, and production costs. Contact us today to find out how we can help you with electrical power switch gear and distribution solutions.